リーン生産方式とは?トヨタ生産方式との違いなどをわかりやすく解説
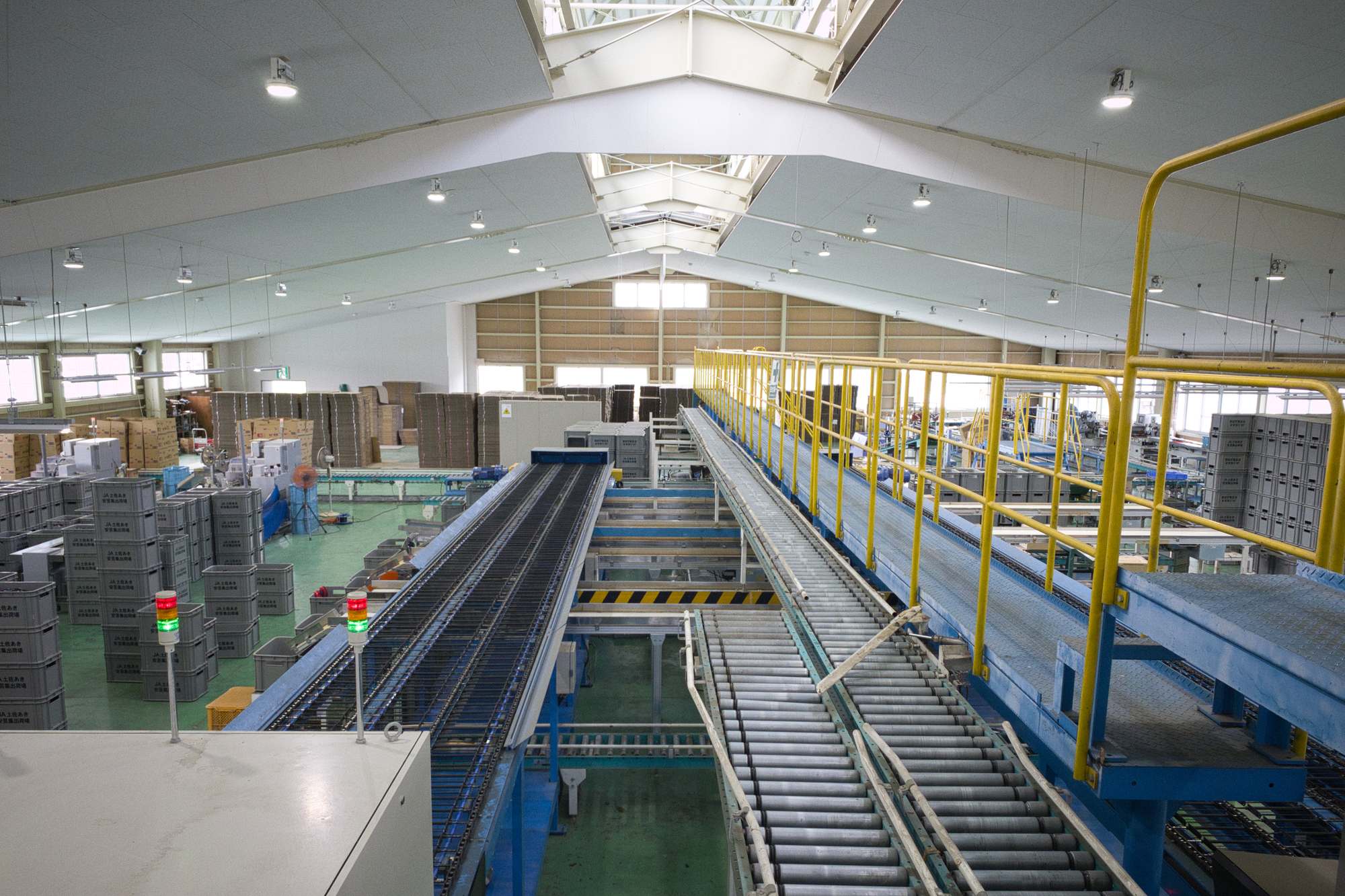
リーン生産方式は、無駄を徹底的に排除し、高品質な製品やサービスを効率的に提供する手法として、世界の多くの企業が採用しています。
その起源は、トヨタ自動車が開発したトヨタ生産方式にあります。
このトヨタ生産方式をさらに一般化し、多様な産業に適用できる手法として進化したものがリーン生産方式です。
この記事では、リーン生産方式の基本概念、導入ステップ、具体的な事例などを紹介します。
ビジネスにおけるリーン生産方式の重要性と活用法について理解を深めたいという方は、ぜひご一読ください。
リーン生産方式とは
リーン生産方式とは、無駄を排除し、高品質な製品を生産するための手法を表します。
リーン生産方式の目的は以下のとおりです。
- 在庫削減
- 業務プロセスの簡素化
- 生産フローの一貫性向上
目的達成のため、従業員の役割と権限を強化し、現場スタッフが改善活動に直接関与するのが大きな特徴です。
トヨタ自動車の「トヨタ生産方式」から発展した方式ですが、現在は自動車生産をはじめとする製造業に限らず、サービス業や物流など幅広い分野で活用されています。
出典)J-Net21「リーン生産方式と従来の生産方式の違いについて教えてください。」
リーン生産方式の意味
lean(リーン)とは、英語で「ぜい肉のない」を意味し、牛肉で言えば「赤身」を表します。よい意味で「無駄がない」「効率的な」状態を表現しているのです。
リーン生産方式は、必要なものを必要な時に必要な分だけ生産する「ジャスト・イン・タイム(JIT)」の考え方が基になっています。
リーン生産方式と従来の生産方式との違い
リーン生産方式と従来の生産方式には、以下のような重要な違いがあります。
影響 | リーン生産方式 | 従来の生産方式 |
無駄の排除 | ・徹底的な排除 ・プロセス効率化 | ・個々の作業に焦点を当てる ・無駄が発生しやすい |
在庫管理 | ・ジャスト・イン・タイム ・過剰在庫を防ぐ | ・需要変動に対応 ・多くの在庫を保有 |
生産フロー | ・ボトルネックを取り除く ・生産時間短縮 | ・大量生産 ・調整不足による滞留発生 |
品質管理 | ・欠陥品の発生予防 ・継続的な改善 | ・製造後の検査に依存 ・欠陥品の対応が遅い |
従業員 | ・現場の改善提案 ・モチベーション向上 | ・トップダウンの指示に従う ・改善提案の機会少 |
組織文化 | ・チームワーク ・組織全体の効率化 | ・縦割りの組織 ・部門間協力が難しい |
こうした違いから、リーン生産方式は、従来の生産方式と比較して効率が高く、結果的に顧客満足度の向上をもたらしています。
リーン生産方式の歴史
第2次世界大戦後、トヨタ自動車は、世界的に有名な自動車会社であるフォードの大量生産に打ち勝つため、戦後の経済復興の中で限られた資源を効率的に使う必要に迫られていました。
そこで生み出されたトヨタ生産方式により、1960~1970年代のアメリカ市場進出がきっかけとなり、トヨタ自動車に注目が集まることになったのです。
1990年になると、アメリカの政治学者ジェームズ・P・ウォマックが出版した書籍「世界を変えた機械」で初めて「リーン生産方式」が登場し、世界中に知られることとなりました。
このリーン生産方式は、トヨタ自動車が実践していた「トヨタ生産方式」を研究し、体系化した結果生まれた方式なのです。
その後も、無駄を排除する効率的な手法が国際的に評価され、世界のさまざまな分野で応用が進みました。
リーン生産方式とトヨタ生産方式との違い
リーン生産方式とトヨタ生産方式は、本質的には類似するものの、応用の範囲が異なります。
トヨタ生産方式は、トヨタ自動車独自の哲学を基にしていますが、リーン生産方式は、それを一般化してどの産業にも適応できるようにしたものです。
リーン生産方式が、世界に受け入れられたのは、多くの分野で役立つことが理解されたからです。
リーン生産方式のメリット
リーン生産方式が世界に広がったのは、多くのメリットがあると認められたからと言えます。主なメリットは以下になります。
- 無駄の排除によるコスト削減
- 生産フローの改善
- 品質向上
- 従業員のエンゲージメント向上
- 環境への配慮
以下で詳しく説明します。
【メリット1】無駄の排除によるコスト削減
リーン生産方式最大のメリットは「無駄の排除」です。「無駄」の中には、過剰在庫、動作、待機時間、欠陥品などが含まれ、生産性を低下させ、コストを増大させる原因となります。
リーン生産方式の導入により、無駄を排除し、コストの大幅な削減が可能で、さまざまな分野に適用可能です。
【メリット2】生産フローの改善
リーン生産方式は、ボトルネックを解消して生産のサイクルタイムを短縮し、プロセスの流れをスムーズにする働きがあります。
この働きにより、製品の市場投入までの時間短縮が可能です。結果的に納期の短縮が可能となり、顧客満足度も向上にもつながります。
【メリット3】品質向上
リーン生産方式は、品質管理を重視しているのが特徴です。品質を向上させるために、標準化された手順や継続的な改善を行って製品の品質を一定に保ちます。
この結果、欠陥品の発生などを未然に防ぎ、製品の価値や信頼性が高まり、市場での競争力も向上します。
【メリット4】従業員のエンゲージメント向上
リーン生産方式では、従業員が積極的に改善提案を行い、意思決定への参加が求められます。
従業員は、役割に誇りと責任を持ち、モチベーションが高まります。これにより、エンゲージメントの向上と離職率の減少につながるのです。
【メリット5】環境への配慮
無駄を排除するリーン生産方式は、資源の節約にも貢献しています。とくに大企業では、1製品あたりの無駄排除がわずかであっても、全体で考えると大きな結果をもたらします。
二酸化炭素の排出量や廃棄物減少に大きく寄与し、持続可能なビジネスモデルの実現につながるでしょう。
リーン生産方式のデメリットと課題
リーン生産方式は、多くのメリットがある一方で、デメリットや課題も存在します。以下のデメリットを理解した上で導入の検討が求められます。
- 需要に対する柔軟性に乏しい
- 導入が難しい
以下で、詳しく説明します。
【デメリット1】需要に対する柔軟性が乏しい
リーン生産方式は、無駄を排除し、在庫を極限まで減らすことを目的とするため、予想外の需要変動に対応する力は弱いと言えます。
また、短期的視点に偏ってしまうと、長期的な投資や研究が後回しになる可能性が否定できません。長い目で見たイノベーション創出という観点では遅れをとることになります。
【デメリット2】導入が難しい
リーン生産方式を導入するためには、企業全体の大変革が必要とされることが考えられます。従来の生産方式からの転換に抵抗が生じるかもしれません。
とくに、それまでトップダウンの管理体制が築かれていた企業では、従業員に自主的な提案を促しても時間がかかることが予想されます。
従業員の教育やプロセスの再設計が求められるため、導入コストや導入時間が大きな負担となる点に注意しましょう。
リーン生産方式を成功に導くための戦略
リーン生産方式を成功に導くには、企業文化としての継続的改善が不可欠です。その中で、以下の戦略が成功のカギを握ります。
- 自働化
- ジャスト・イン・タイム
- かんばん方式
- 5S活動
- 標準化
これらを詳しく見ていきます。
1.自働化
自働化は、リーン生産方式を支える重要な概念で、人間の介入なしにコンピュータが不良を察知し、生産プロセスを止める仕組みです。
自働化により製品の質向上と無駄の排除が実現できますが、同時に自動化を行う機械やコンピュータの定期的なメンテナンスが必要です。
また、従業員に対しても適切な教育やトレーニングを行い、監視能力を強化する必要もあります。
2.ジャスト・イン・タイム
ジャスト・イン・タイムは、必要なものを必要な時に必要な分だけ生産することを目的とした戦略です。
ジャスト・イン・タイムにより、在庫を最小限に抑えて資源を効率的に使用できますが、一方でサプライチェーンの協力と連携が必須となります。
サプライヤーとの情報共有を密に行い、需要を正確に予測できれば、過剰生産もしくは過不足の防止が可能です。
3.かんばん方式
かんばん方式では、各工程が「かんばん」と呼ばれるカードを用い、必要な部品や材料の供給を指示します。これにより、過剰在庫を避けつつ生産効率を最大化できます。
ジャスト・イン・タイム同様に、必要なものを必要な時に供給する仕組みを整えます。
4.5S活動
5S活動とは、整理、整頓、清掃、清潔、しつけの5つを実践する活動です。この5S活動の実践は、職場環境を整え、生産効率を向上できます。
作業の流れをスムーズにし、無駄の削減が実現できるだけでなく、従業員の意識も向上します。
5.標準化
標準化とは、作業手順やプロセスを一貫して実施するための基準を設けることを表します。標準化により、作業のばらつきを防ぎ、品質を一定に保ちます。
新しい従業員の教育が容易になると同時に、プロセス改善も進めやすくなるのがメリットです。
リーン生産方式の導入ステップ
リーン生産方式を効率的に導入するには、以下のステップが必要です。
- 問題の把握
- 分析
- 改善策の決定
- 無駄の排除
これらのステップについて、詳しく見ていきます。
【ステップ1】問題の把握
リーン生産方式導入を成功させる第一歩は、現状の課題の正確な把握です。全体のフローを見直し、どこに無駄が生じているかの特定が最も重要です。
- 従業員からのフィードバックを受け、日々の業務にある課題を集める
- ボトルネックとなっている箇所を特定し、生産性や品質に与える影響を明確にする
【ステップ2】分析
次は、ステップ1で把握した課題を詳細に分析するステップです。具体的には、データ収集を行い、根本的な原因を明らかにします。
- 不良品や欠陥品が発生している箇所や過剰在庫の原因となっている箇所を分析
- 作業時間や動線を分析して効率化できる箇所を見つけ出す
【ステップ3】改善策の決定
ステップ3では、分析結果に基づく改善策を決定します。企業全体が協力し、具体的で実現可能な改善策を策定する必要があります。
- 作業手順の標準化、新たな技術導入、従業員への教育・トレーニングなど
- 改善策を実行するために適切なコミュニケーションを図る
【ステップ4】無駄の排除
最後のステップでようやくリーン生産方式が導入され、無駄の排除が可能となります。
- 改善策を実行し、モニタリングを行う
- 継続的な監視と改善を繰り返す
- 成功事例を共有し、ほかのプロセスに応用していく
以上のステップを経て、リーン生産方式は作業の効率化だけでなく、企業の競争力を高める手段となります。
リーン生産方式の具体例
リーン生産方式は、製造業だけでなく、サービス業や航空業界のような高度な技術を要する分野においても活用されています。
リーン生産方式が長期的な成長と競争力確保に大きな貢献をしている事例を、以下で紹介します。
スターバックスでの導入事例
世界中でカフェを展開するスターバックスは、リーン生産方式を導入して店舗運営の効率化とサービス向上を実現しました。
バリスタの作業効率を高めるため、顧客が注文したドリンクが効率的かつ迅速に提供されるよう、店舗内の業務フローを徹底的に見直しました。これにより、待ち時間の大幅な短縮に成功しています。
また、必要な材料を必要な時に確保して、無駄な在庫を省いています。
デルでの導入事例
コンピュータ機器を生産・販売するデルは、リーン生産方式を導入して大幅な業務効率化を達成しました。
ジャスト・イン・タイムの概念を取り入れた「ビルド・トゥ・オーダー」方式で、パソコンのオーダーをオンラインから先に受け取り、あとから必要な部品を調達しています。
この方法で在庫を最小限に抑え、顧客ニーズに応じた製品を迅速に製造できるのです。
ボーイングでの導入事例
航空機を製造するボーイング社は、航空機の生産プロセスにリーン生産方式を導入して革新しました。
とくに「かんばん方式」を採用し、組み立てラインを再設計しました。これにより、各工程の流れをよりスムーズにし、生産性を大幅に向上させています。
航空機の納期を短縮し、顧客の需要に迅速に応えることができるようになりました。同時に品質管理も強化され、航空機の信頼性を高めています。
まとめ
リーン生産方式は、トヨタ生産方式から発展した、無駄を排除して効率的に高品質な製品やサービスを生み出す手法です。現代においては、製造業のみならず、ほかの分野でも広く活用されています。
在庫管理の徹底や品質向上を図りつつ、従業員の直接の関与を促し、組織全体の生産性を向上させています。
ただし、大がかりな変革を必要とするため、中小企業で導入するのは骨の折れる作業であることは否定できません。
効率的にリーン生産方式を導入するため、実現可能なところから取り組んでいきましょう。
関連記事
-
ビジネスモデルとは?種類や具体的な作り方、フレームワークを簡単に解説!
ビジネスモデルは、事業の価値提供の仕組みと収益化の方法を示す設計図です。本記事では、ビジネスモデルの基本的な構成要素から、実際の作り方、成功事例まで詳しく解説します。
-
予実管理の目的を理解して経営を効率化!成功事例から学ぶ中小企業の戦略
昨今のビジネス環境において、経営の「見える化」は避けて通れない課題となっています。とくに中小企業では、限られた経営資源を最大限に活用するため、売上や利益、コストといった数値の適切な管理が重要です。そこで注目されているのが「予実管理」です。本記事では、中小企業における予実管理の基本から実践的なポイントまで、分かりやすく解説していきます。
-
個人情報が漏洩した場合の対応は?罰則・事例・企業が取るべき対策を解説
デジタル化が急速に進む現代社会において、企業が取り扱う個人情報の量は増大し、その価値はかつてなく高まっています。
その一方で、個人情報の漏洩事件は後を絶たず、ひとたび発生すれば企業の信頼を根底から揺るがしかねない重大な経営リスクとなります。
そこでこの記事では、個人情報が漏洩する主な原因から、漏洩時に企業に課せられる報告義務、そして厳しい罰則の内容までを詳しく解説しますので、ぜひ参考にしてください。
-
再生可能エネルギーとは?種類・メリットやデメリットについて解説
近年、地球温暖化や化石燃料の枯渇が世界的な課題として取り上げられる中、再生可能エネルギーの導入が注目されています。
しかし、再生可能エネルギーにはメリットだけでなく、実はデメリットも存在することをご存じでしょうか。
この記事では、再生可能エネルギーの基本的な概念から、主な種類、導入のメリット・デメリットなどについて詳しく解説していきますので、是非参考にしてください。 -
グランドデザインとは?ビジネスシーンやITシステムでの意味を解説
ビジネスやテクノロジーの急速な進化がある中、「グランドデザイン」という概念に注目が集まっています。しかし、このグランドデザインという言葉の本質的な意味、各分野での活用方法を十分に理解している人は少ないと言えるでしょう。この記事は、グランドデザインとは何か、どのような意味を持つのか、その重要性や活用例について詳しく解説します。